OCP System
OCP is developing an orbital infrastructure, which reduces the reliance on material from Earth, for the construction of large orbital structures. The development includes both a material consisting of a polymer binder combined with lunar regolith and additive manufacturing processes for the on-orbit manufacturing of structural components. Our goal for the infrastructure is to manufacture hexagonal, circular, pentagonal, and square panels that are up to 100 meters across, along with beams that have customer specified lengths for use in the construction of persistent human occupied structures (250 m diameter minimum) and sensor / detector / defeat platforms that can a have a span greater than 250 m.
Our approach is not limited by launch vehicle constraints, the raw materials are lifted to space as bulk items. The payload size and shape constraints of a launch vehicle are negated as the items will be in the form of liquids, gases and powders which will fill any shape container. The only constraint will be the mass the launcher can carry. The manufactured components are now constrained by the manufacturing facility, which can be expanded over time, and not by a lift vehicle.
The use of polymers as binders allows for the material to fit the missions. Different polymers have different strengths, radiation resistance / blocking and flexibility capabilities, the mission and / or placement of the component will determine what polymer properties are needed. The use of polymers also provides the ability to “glue” the panels together for large structures and for easy repair / refurbishment.
The additive manufacturing printers will be completely different from their terrestrial counterparts. A printer that is 150 to 200 m across and free floating in orbit will be very sensitive to Newton’s third law of motion: Action and Reaction. Each movement of a “print head” or “table” will have to be countered with an equal but opposite force. The design must focus the forces of printing in one direction, allowing for a single opposite direction force to bring the system into equilibrium. The OCP printer design meets these requirements and has a patent pending.
Material
The OCP program has its foundation in the ancient past. As outlined in a paper [1] from the Geopolymer Institute, the Tiahuanaco monuments (Tiwanaku / Pumapunku) in Bolivia and possibly the Egyptian pyramids were built using a polymer / rock dust system similar to what we are proposing. However, instead of using molds and water, as the ancients did, we will use additive manufacturing and a waterless process.
Our main goal, for all brands of Stellamer, is to use at least 70% of in-situ products by mass. In most versions of Stellamer, the mass can be any dry mass including regolith, dirt, or any other material from a celestial body.
Two broad categories of Stellamer are being developed: Stellamer-P and Stellamer-R. Stellamer-R is designed for use in a gravity environment and has superior compression strength, while Stellamer-P is for use in a micro-gravity environment with excellent tensile strength and able to withstand impacts of micrometeors.
Stellamer-P
Stellamer-P is designed for structures in space that may be subject to micro-meteoroids, thermal and mechanical stresses. It has a higher tensile strength than Stellamer-R and can be used for pressure vessels. The construction of a pressure vessel would use a tri-layer approach. A ballistic gel like adhesive would be sandwiched between an outer layer that is semi-flexible and a rigid inner layer. If the outer layer is penetrated, the middle layer will seep into the breach and harden when exposed to sunlight, providing a minor self-heal capability.
Stellamer-P will be used in manufacturing processes in microgravity. Liquids in microgravity form balls due to surface tension. Since Stellamer-P is a high viscous liquid, it will be subject to surface tension which could adversely affect the printed shape. To prevent this a UV activator is added that, when exposed to UV, forms a thick surface skin, negating surface tension.
Goals
The initial goals for Stellamer-P are:
- Waterless process that can be used in additive manufacturing.
- Compose 70% of in-situ products, by weight. Basalt is substituted for regolith in initial tests.
- Withstand slow speed impact (< 16 kph)
- Stop impacts from small space debris
- Have a tensile strength > 200 kPa.
- Demonstrate the capability to maintain printed shape in microgravity before full cure.
Testing
All test samples are molded into hexagonal shapes with a side length of 79.73 mm and a thickness of 12.78 mm. The layers in a three-layer construction have the designation of “A”, “B”, and “C”, starting with the outermost layer “A”, (the layer that is exposed to the space environment) and proceeding to the innermost layer “C”, which is used for the construction of pressure vessels.
All tests were conducted at room temperature.
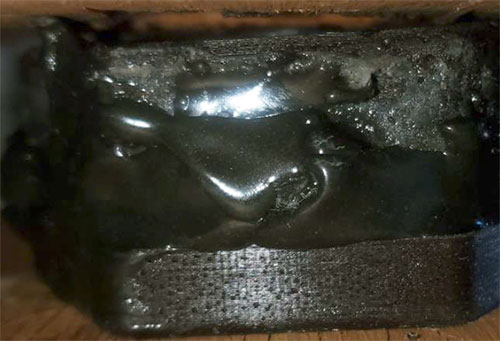
To simulate a micrometeor impact on layers A and C, we used a .22 rifle at 38 yards. The first test used Winchester 555 varmint rounds; a 36-grain jacketed hollow point with a muzzle velocity of 390 m/s (1280 fps). The second test used Blazer 22 a 40-grain bullet with a muzzle velocity of 376 m/s (1235 fps). To pass this test, the sample may allow the bullet to pass, but the sample must remain intact, with little to no cracking and material loss.
Tensile strength was measured using a manual tensioner with a digital force meter. The test articles had a surface area of approximately 10 cm2.
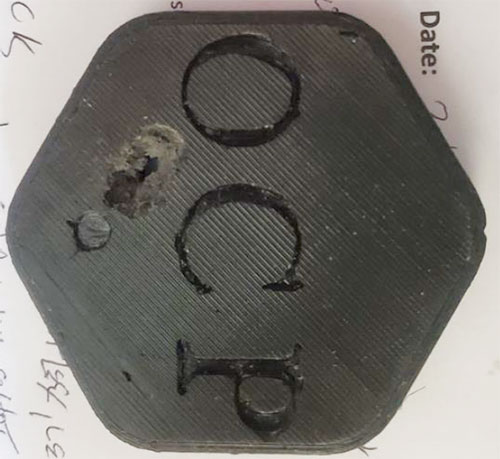
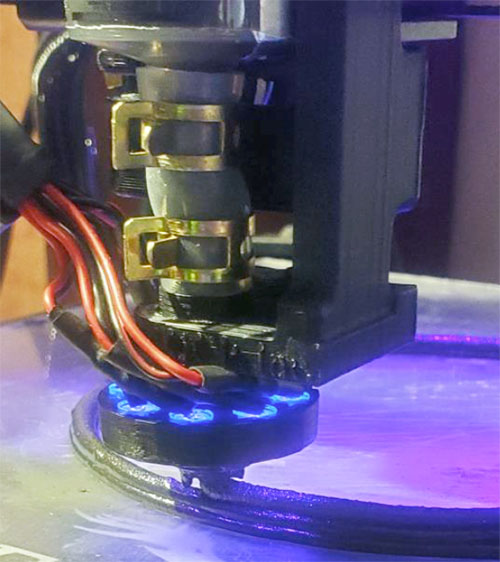
Layers A and C are subject to a slow speed impact test. A 1 kg steel ball is dropped from a height of 1.5 m. The sample is supported at the edges and must remain intact after the impact with little or no cracking.
The three-layer sandwich is evaluated using the micrometeor and impact tests. The micrometeor and impact tests are done in the same manner, however the bullet must not pass through, and the C layer must be intact and undamaged.
The printing test uses a modified 3D printer extruding Stellamer-P. To pass the test the printer must be able to make multiple passes, creating a wall that can support itself and maintain its shape against gravity.
Results
- All final test articles were made with 70% basalt by weight.
- Space debris test – The three-layer test sample was able to stop both types of bullets without damage to the C layer.
- Slow impact test – Layers A and C withstood impact from 1.5 m with no damage or marks.
- Tension testing – Values are averages:
- Layer A – 531 kPa
- Layer B – 350 kPa
- Layer C – 865 kPa
- Printer testing – Successfully printed multiple layers. UV curing agent prevented running and slumping of material.
All goals were met or exceeded resulting in successful proof-of-concept.
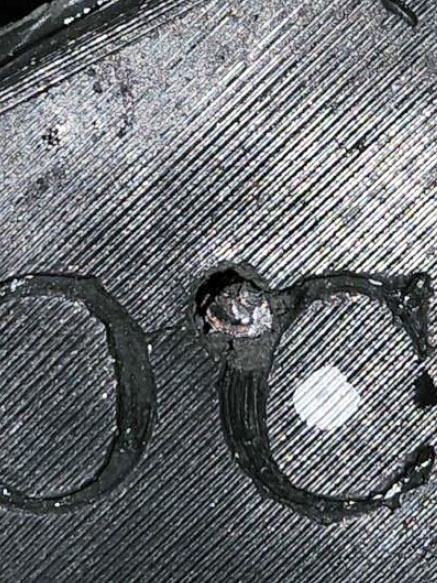
References
- Tiahuanaco monuments (Tiwanaku / Pumapunku) in Bolivia are made of geopolymer artificial stones created 1400 years ago. Archaeological Paper #Keng, Geopolymer Institute Library, J. Davidovits, L. Huaman, R. Davidovits, (2019), www.geopolymer.org. DOI: 10.13140/RG.2.2.31223.16800.